|
Website : Home >> Products |
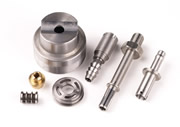 |
|
CNC Turning
We have experience in rough turning blanks and finish turned parts with close tolerance I.D. & O.D. features. We have found that in some cases hard turning is an economically viable alternative to grinding for size and finish.
As well as bar turning, we can turn forgings, fine blanks and aluminum castings. We can machine most ferrous and non ferrous materials on the market. The list includes aluminum, brass, ceramic, copper, plastics, carbon steel, alloy steel, stainless steel and tool steel.
From blanking to finished machining, we are dedicated to providing you with a quality part that meets your needs in a timely manner.
|
[view more] |
|
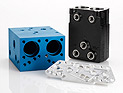 |
|
CNC Milling
We use state of the art CNC Vertical and Horizontal Machining Centers to manufacture parts to specification. We regularly invest in new equipment while maintaining existing equipment through a preventative maintenance program. We operate some of the most trusted machine tools in the industry. The equipment is equipped with high pressure coolant systems to maximize efficiencies, tolerances, and surface finished. Additionally, the equipment is interfaced with rotary indexers resulting in complex machining capabilities.
Computer controlled or CNC milling is a process used to machine component parts from solid materials in both horizontal and vertical form, depending on the orientation of the spindle. In the milling process, both the cutter and the workpiece are moved with precise control to less than 0.001 in (0.025 mm), usually by means of precision ground slides and lead screws or a similar technology.
CNC milling machines perform a wide range of operations ranging from simple cutting to complex contouring. Cutting fluid to typically used with CNC milling machines to cool and lubricate the work surface.
|
[view more] |
|
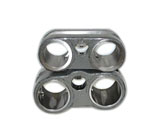 |
|
Casting & Forging Parts
Equipped with sophisticated, multi-axis CNC lathes & CNC machine centers, we can turn, mill, bore, tap, and drill all types of casting and forgings. Machining gray or ductile iron casting to lightweight aluminum forgings for industrial applications to high strength iron and steel forgings, chassis parts, as well as crankshafts, is not a problem for us.
Typically, there are no limits to the size/weight/shape of parts machined by us. From basic to complex operations, we precisely meet our customer’s prototype, short run, and high volume production quantity requirements. CNC machining for castings and forgings, meet/exceed client’s design tolerances of up to 0.0004”.
Designing, engineering, and manufacturing tools in-house reduce the set up time and helps in quick turn around. We also offer broaching, grinding, stamping, and other surface finishing services for machined castings as well as forgings, according to customer requirements.
|
[view more] |
|
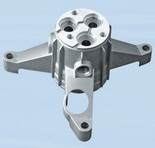 |
|
Aluminum Die Casting
Aluminum alloy is lightweight, yet it possesses high dimensional stability making complex shapes and thin walls easily attainable. Aluminum has good corrosion resistance and mechanical properties, high thermal and electrical conductivity, as well as strength at high temperatures.
The fact that an aluminum die casting is lightweight is obvious. Not so obvious is that parts die cast of aluminum can withstand the highest operating temperatures of all the die cast alloys. The strength, rigidity and corrosive resistance of aluminum die castings offer significant heat dissipating advantages.
Consider These Aluminum Alloy Advantages:
Highest Operating Temperatures
Very good corrosion resistance
Light-weight
Excellent strength and hardness
Very good thermal conductivity
High Electrical conductivity
Good finishing characteristics
|
[view more] |
|
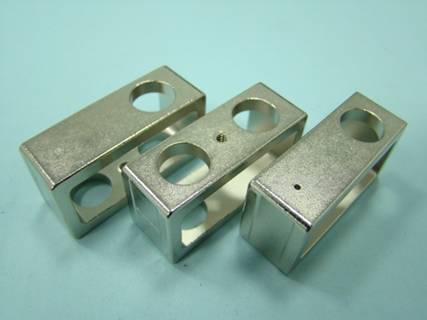 |
|
Zinc Die Casting
Zinc is, by far, the easiest alloy to use in the die cast process. It offers high ductility, high impact strength and is most easily plated. A zinc die casting is economical for small parts, has a relatively low melting point and promotes long die life.
Zinc alloys take plating very well. That makes zinc die cast parts ideal for aesthetic applications.
Zinc’s high strength and hardness make it the ideal alternative to machined, pressed, stamped and fabricated items. Zinc’s properties make it a perfect solution in countless situations and uses.
Consider These Zinc Alloy Advantages:
High strength and hardness
Very good electrical conductivity
High thermal conductivity
Low cost
Very good quality finishing characteristics
Excellent corrosion resistance
|
[view more] |
|
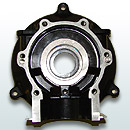 |
|
Magnesium Die Casting
When saving weight is absolutely necessary, magnesium die casting is the ideal choice. Magnesium possesses the lowest density of all structural metals. As lightweight as some plastics, magnesium has the decided advantage of greater strength and rigidity. Moreover, magnesium offers inherent EMI/RFI shielding, durability, heat-dissipation and is fully recyclable.
Magnesium Alloy Characteristics:
The lightest of all structural metals – 35% lighter than aluminum, and 75% lighter than steel.
Excellent stiffness and strength-to-weight ratio
Outstanding EMI & RFI shielding properties
High conductivity, electrical and thermal
Withstands high operating temperatures
Cost-effective compared with many engineered thermoplastic materials
High dimensional accuracy and stability
Exceptional thin wall capability
Good environmental corrosion resistance
Good finishing characteristics
Fully recyclable
The castability of magnesium die casting is excellent. These are the standard alloys.
Alloy: AZ91D
The most common alloy used in high pressure die casting
AZ91D offers good strength/weight ratio and excellent castability
Alloy: AM60B
|
[view more] |
|
|